IronCAD is unique and the most productive
conceptual 3D CAD system. Change is incredibly easy. You can have
several iteration of your design in the same file.
- Single Model Environment - Parts and
assemblies in a single file
- Drag and Drop Design from Custom or
Standard Catalogs
- The Only Integrated History/Direct
Edit Design - Both used in your design process
- Copy and Paste Directly from Different
Files
- The Incredible Feature, Part and
Assembly Manipulator - The Triball
We have the native IronCAD and STEP File Available here for download
Note: IronCAD Model .ics/AID .icd native
files must be copied to the same folder.
3D Modeling is the basis for our
engineering. That is the only place where productivity is paramount.
You can have all the PLM/MBE gurus debating data management, but it
does not add one smidgeon of productivity to the design process.
Top down or In-Context modeling is the most productive
feature of 3D CAD. Most systems tout this but each part is still an
external part. We are talking about a single model or multi-object
design environment. Both of the systems we represent offer this as
the "normal" design process. Thereby increasing your productivity 20
to 30%.
In these exercises I not only focus on modeling techniques, but
also on much more productive systems to do our designs. I hope you
enjoy them and learn something. If you are in management, understand
that all 3D CAD systems are not the same. Cutting your engineering
costs is very simple. Even your legacy data is not a problem. Please
feel free to give me a call. There are millions of man hours wasted
every day with poor modeling techniques and dated 3D CAD
systems that cost a fortune. Productive 3D CAD systems do not have
to be expensive.
Joe Brouwer
206-842-0360
I am doing the below assembly for
an exercise showing my modeling techniques and, of course, my 3D CAD
solutions.
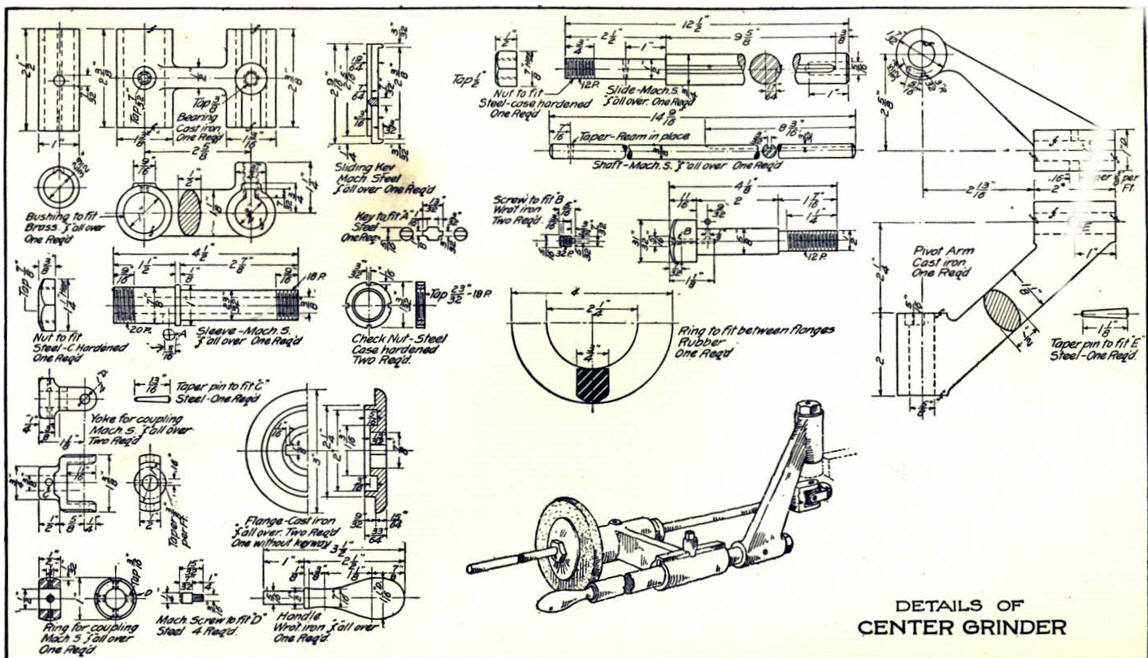
When I introduce IronCAD's very
flexible design paradigm I have a hard time to get the Pro/e clone
users, like Solidworks and other programs to understand the drag and
drop design paradigm.
I saw some video challenges on linkedin and thought I would give it a
try on IronCAD. This will give you an idea how different
and flexible IronCAD is compared to the conventional Pro/e clone and
to the not so conventional Fusion 360.
These exercises started out to show the benefits of IronCAD over Fusion 360, but
quickly turned into a study of modeling techniques. Take a look at all of
them, they will open your eyes to a much different and more productive way of
modeling. It really has more to do with modeling technique than it has to do
with the 3D CAD systems. I have found that I do 3D modeling as compared to
the conventional 2D sketching. Of course, having a more productive 3D CAD
system doesn't hurt.
See the
comparison with many other 3D CAD systems.
3D CAD Modeling Techniques
These exercises were incredibly
popular and I thought I would follow up by showing more examples of
this 3D modeling technique.
We will be doing a
couple of parts each weekend in both IronCAD and ZW3D. I hope you
enjoy these exercises and hopefully they may lead to increasing your
productivity.
We will start with the Bearing.
The first thing we
will do is drag a cylinder from the catalog and size it.
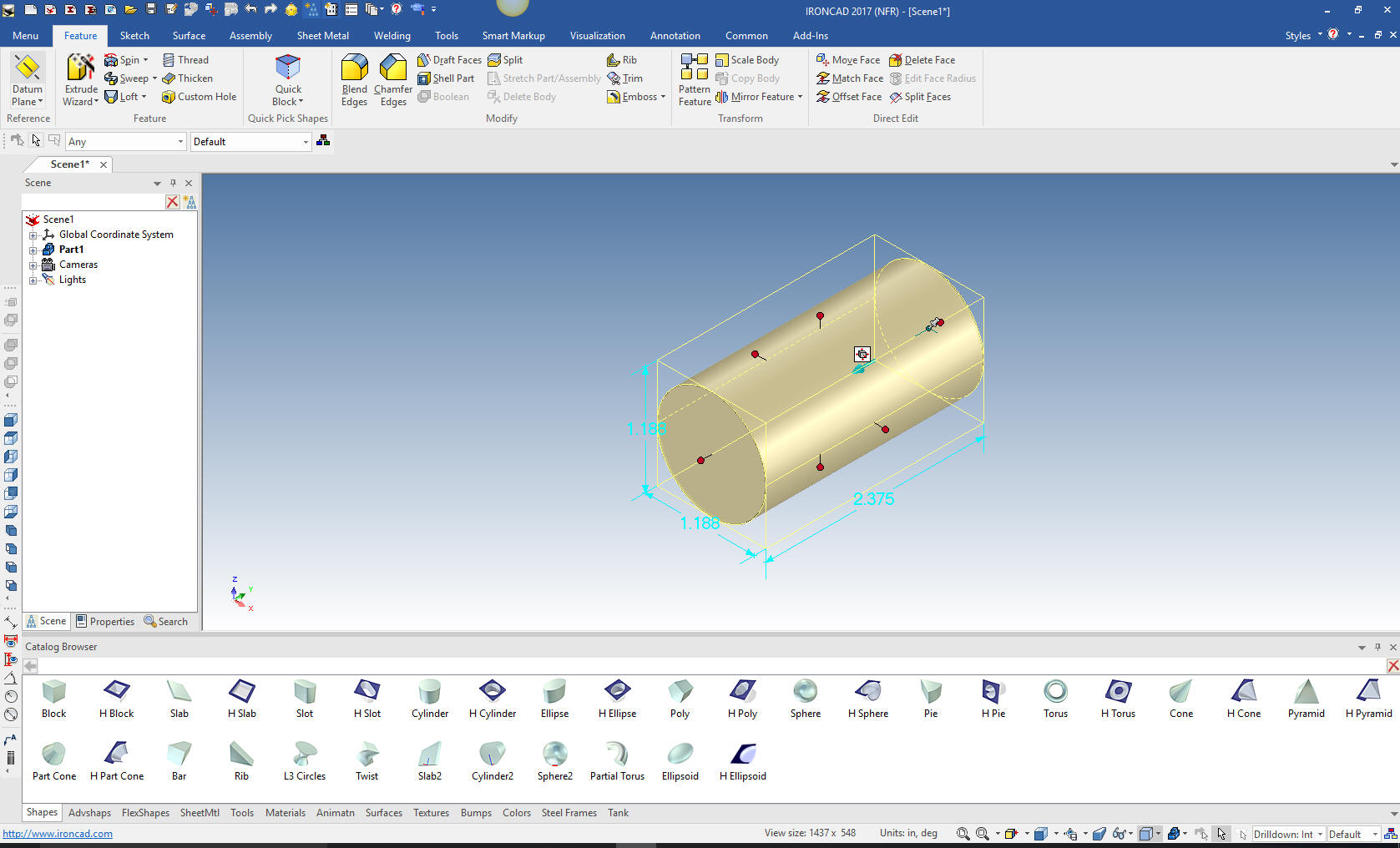
We will now drag another cylinder on to
the end of the existing cylinder. This is a bit unorthodox but we
want to make sure that it is a single part. Due to the single model
environment you can not have two separate part as one unless we
connect them or Boolean them. I want to eliminate that step.
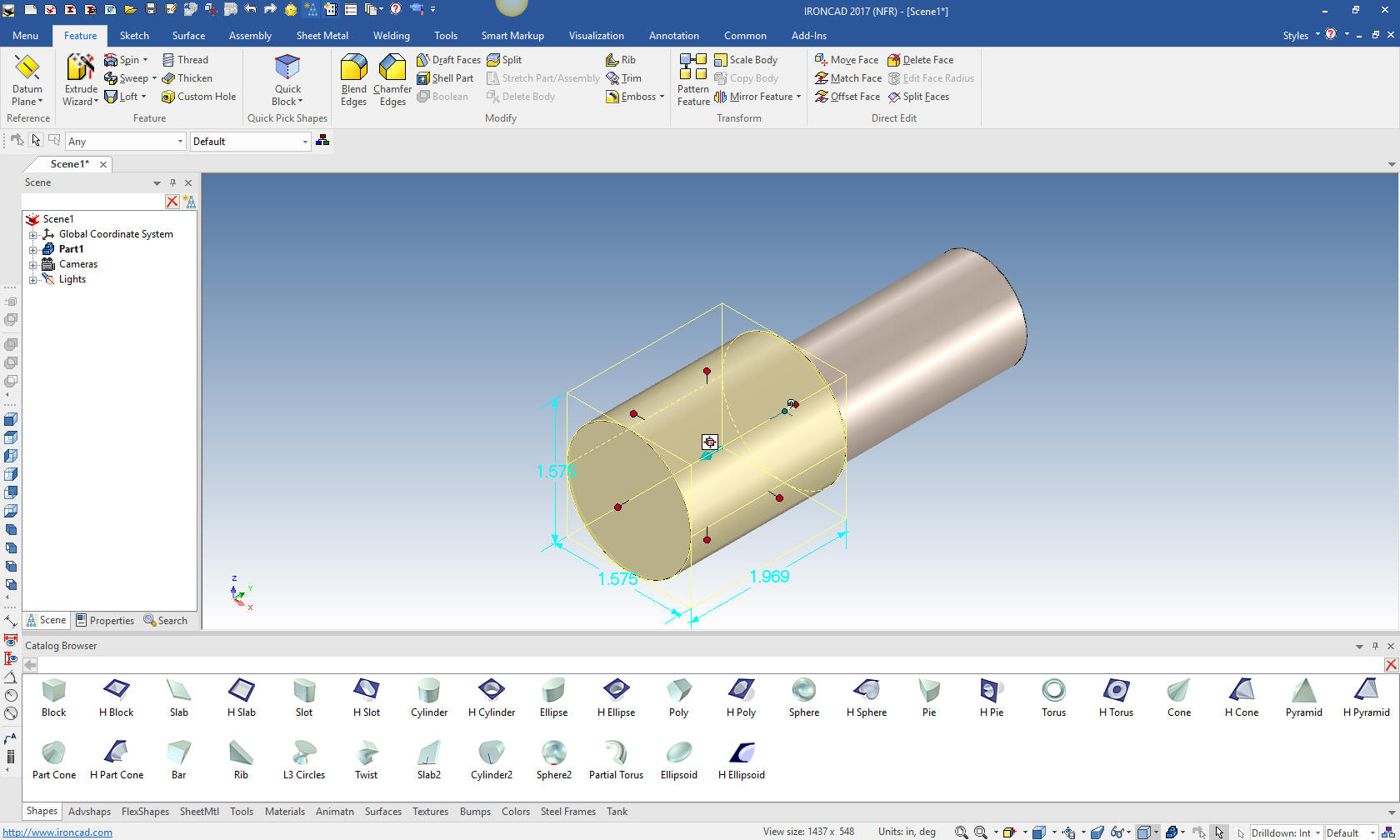
We will now use the triball and move it
into place. The catalog can be set to autohide to increase the
design scene work area.

I will show this view to indicate these two cylinders are one part.
In IronCAD you have different levels of selection. Yellow is the
assembly, Blue is the part, Yellow again is the feature (negative or
positive) and green is the face or surface.

Now for the ellipse I drag the ellipse on a face of the cylinder and
size it by selecting a handle with a click on the right mouse button
which brings up the dialog box. This makes the ellipse a feature of
this part.
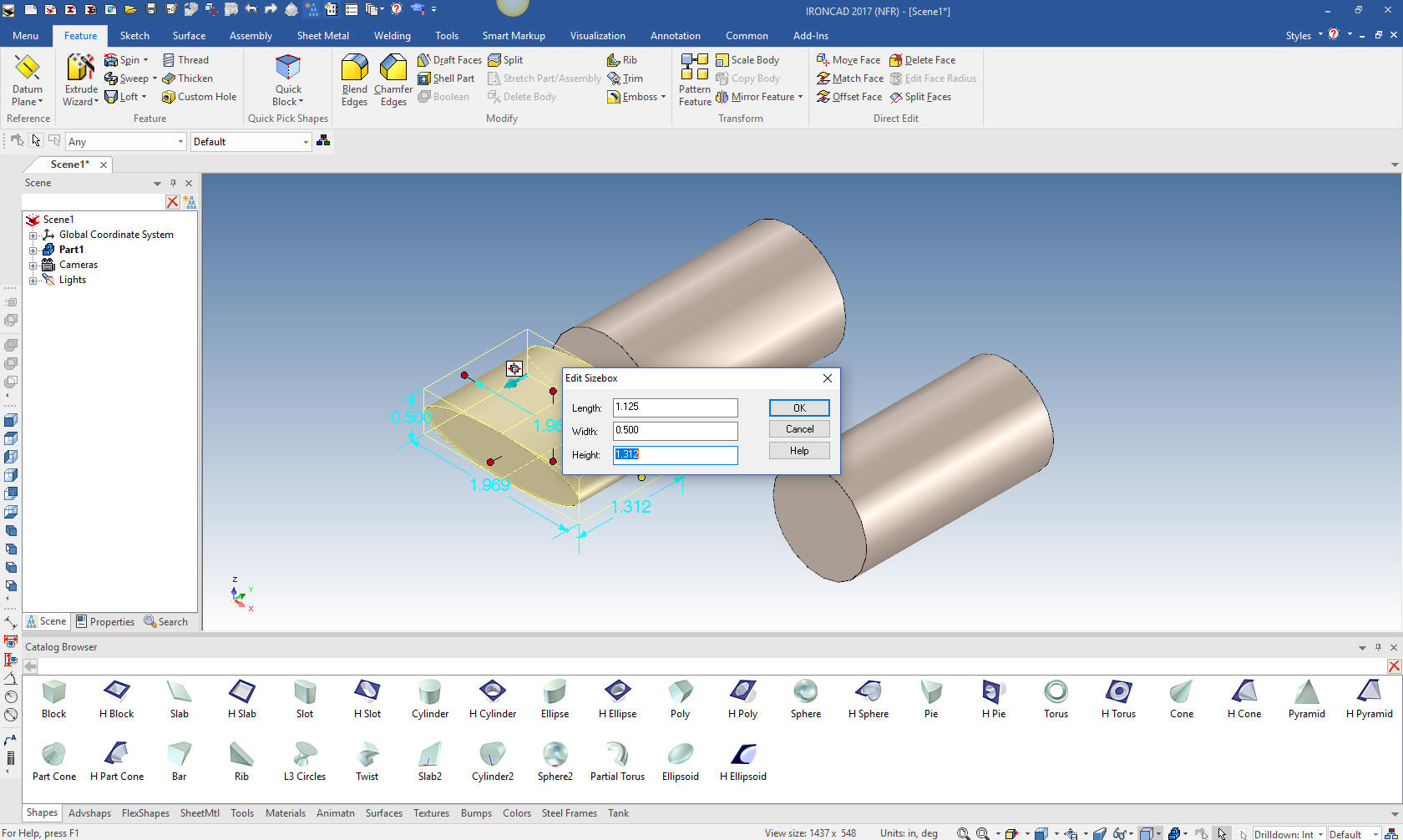
Again using the triball I locate the ellipse and pull it into place.

With that done now for the vertical bosses. Again we drag a cylinder
on to the end and center of the existing right cylinder and size it.

Using the triball we rotate it and move it into place.

Using the triball will now copy (we
can copy, link or pattern) the
cylinder and size it. Since it is based on the center of the
cylinder we can just set the height. We copy since are going to
modify it. Linking would create a duplicate which would reflect any
changes to either feature. Pattern of course needs no explanation.
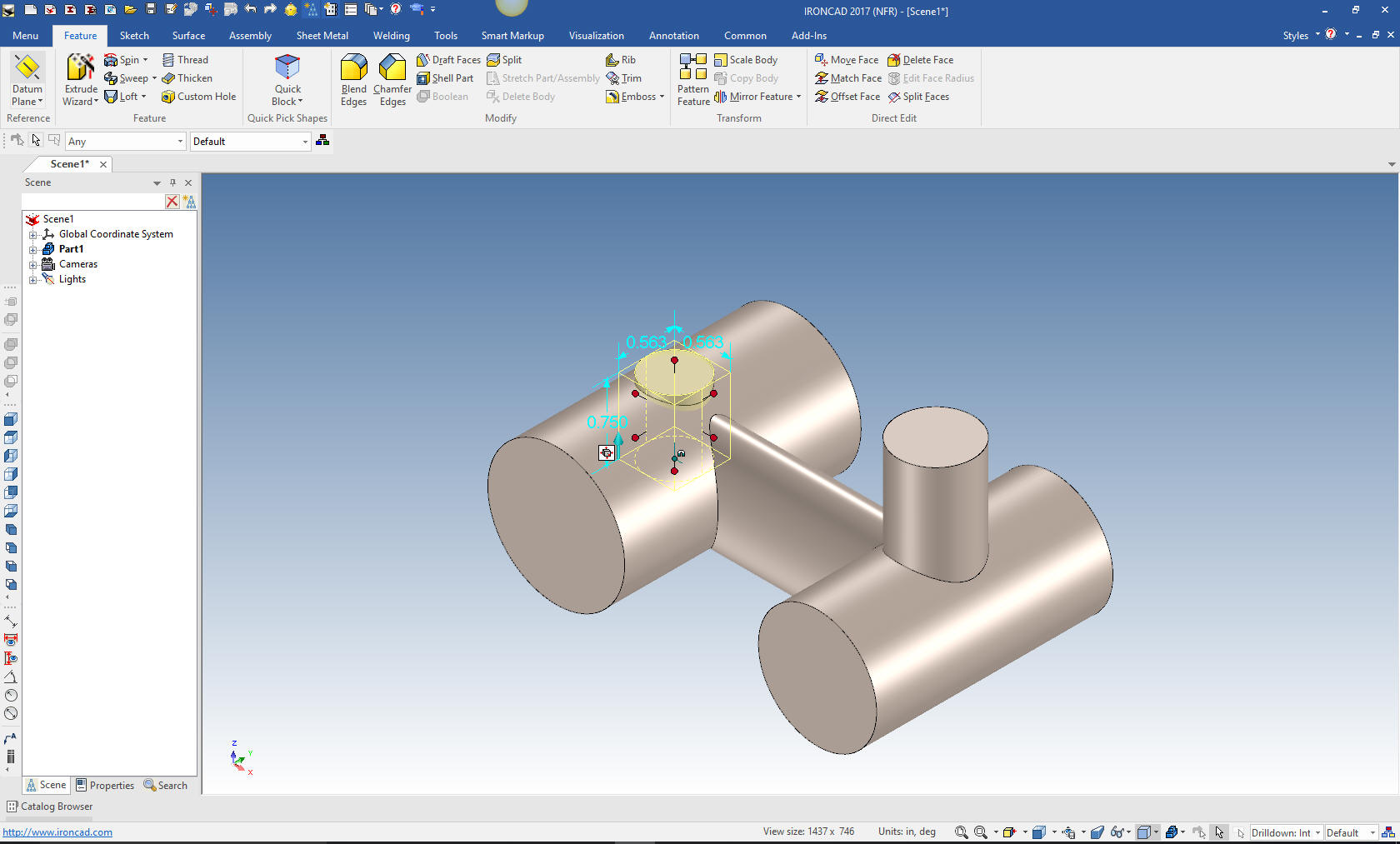
Now the shape for the slot. I drag a block on to the center of the
cylinder. We can then grab both handles and create a symmetrical
block. So easy. We snap the bottom of the block at the center of the
cylinder then just set the height.

Now we just pull the shape into place.
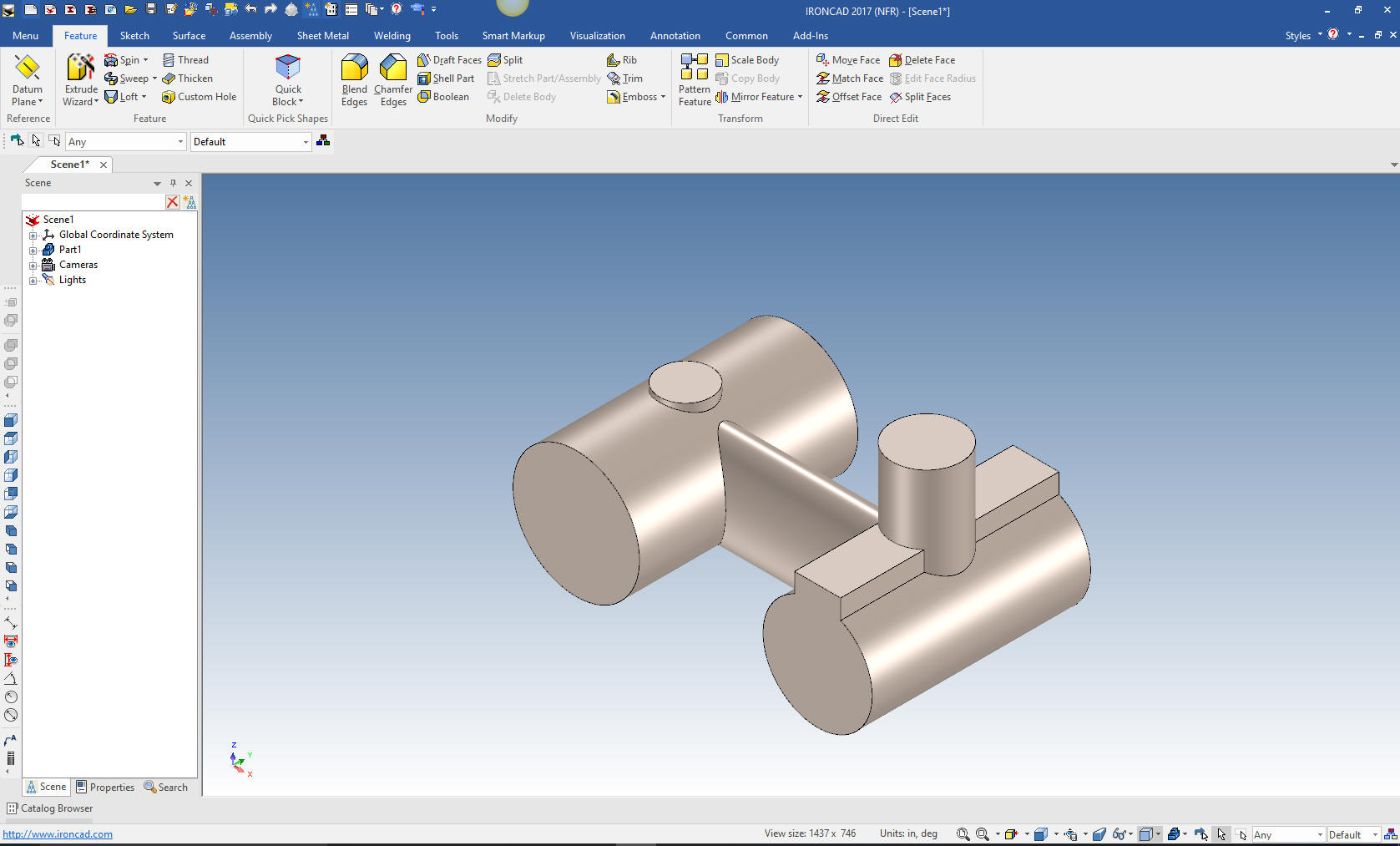
Now we
create the holes in the cylinder by dragging hole cylinders on the
face of the existing cylinders and sizing them. IronCAD offers
points that are on the ends, midpoints and centers of circles for
easy placing of shapes.

Now the cut for the sliding key slot. We will drag a hole block to
the center of the face and size it with the handle snapping to edges
and corners.
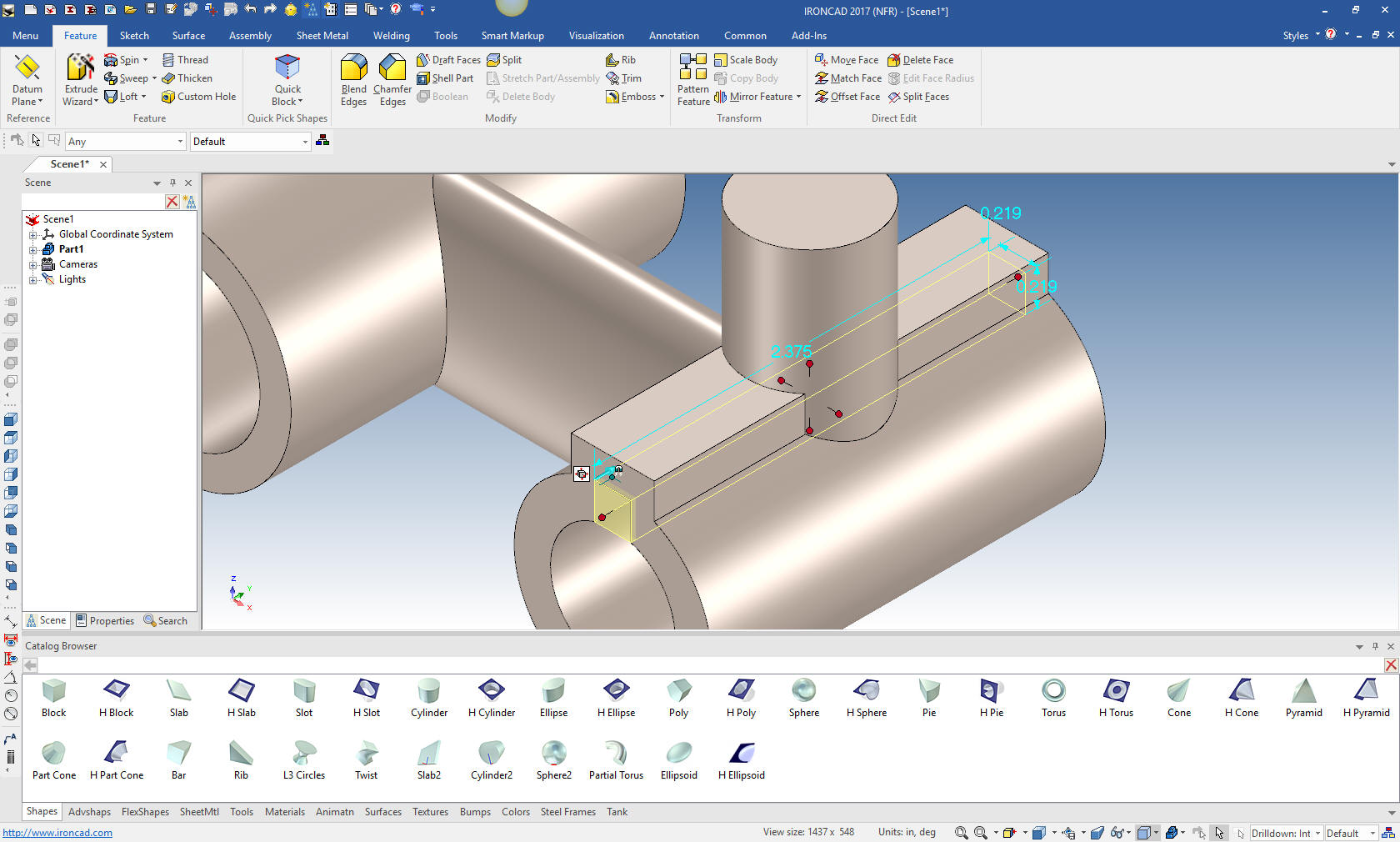
Now for the tapped holes. From the tool catalog we drag the custom
hole tool to the center of the affected cylinder.

Now for the blends. Blends are almost always put in last. They
should be thought through on how to put them in. I will go through
the process I think best in this application.
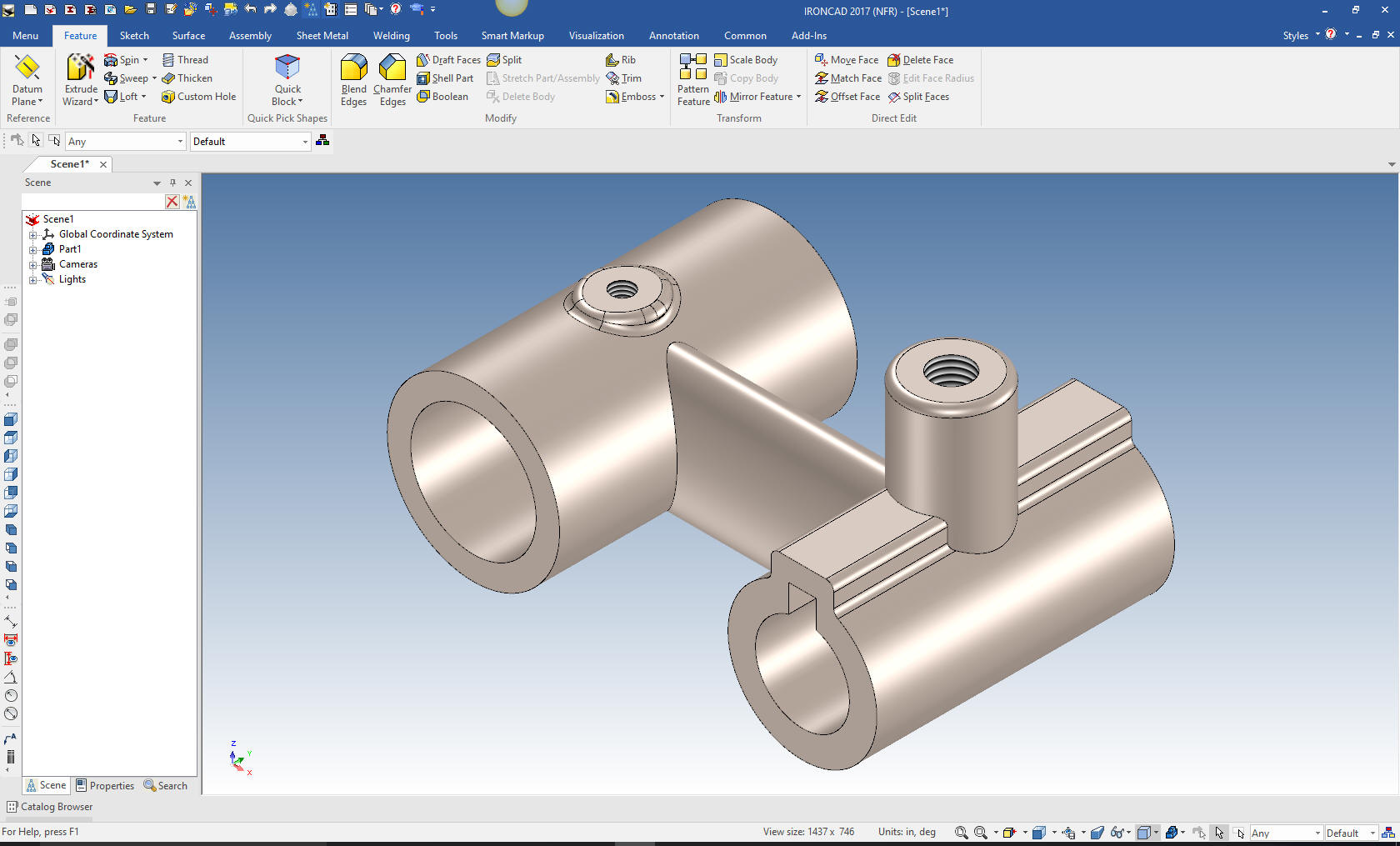
Then he final blends.

The
part is complete. NO SKETCHES, NO CONSTRAINS! This is what I call 3D
modeling. It is much, much faster.
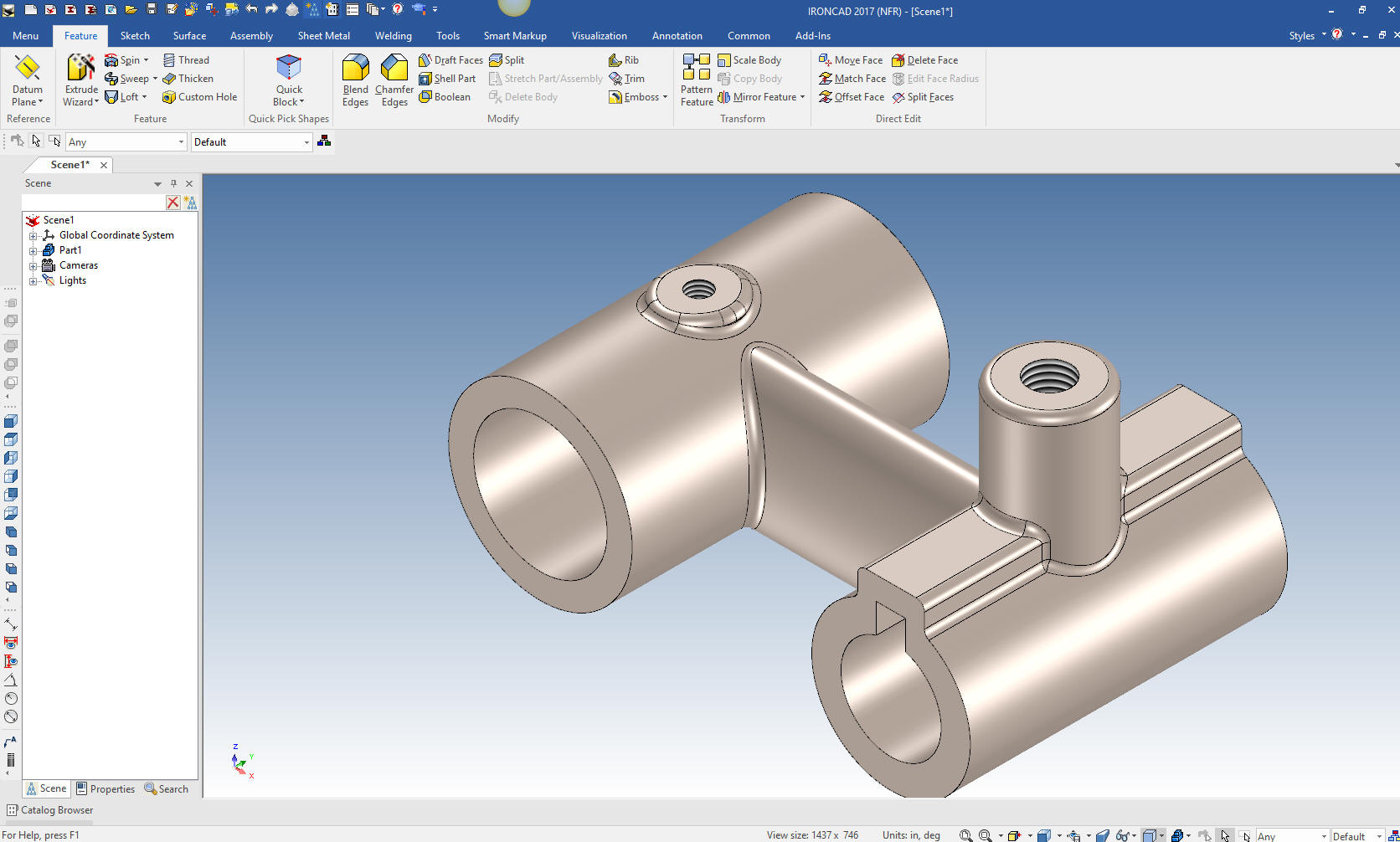
The
increased modeling productivity is just one aspect of IronCAD over
the popular 3D Clones. Next week we will start adding parts and
showing the advantage of the single model environment.
We
will now detail this part for clarity incase you would like to
follow along in your own system. Since IronCAD is a single model
environment we need to define the configuration so when we detail
the parts we can define them in the drawing module. We will name
this configuration Bearing. This will make more sense as we turn
this into an assembly just by adding parts. We will be detailing all
of the parts in one document file.

Oops I
just realized I put in the wrong height for the tall boss. I will
just change the height of the base cylinder. Problem solved! This
shows you how easy it is to make a small change in the model if you
make a mistake.
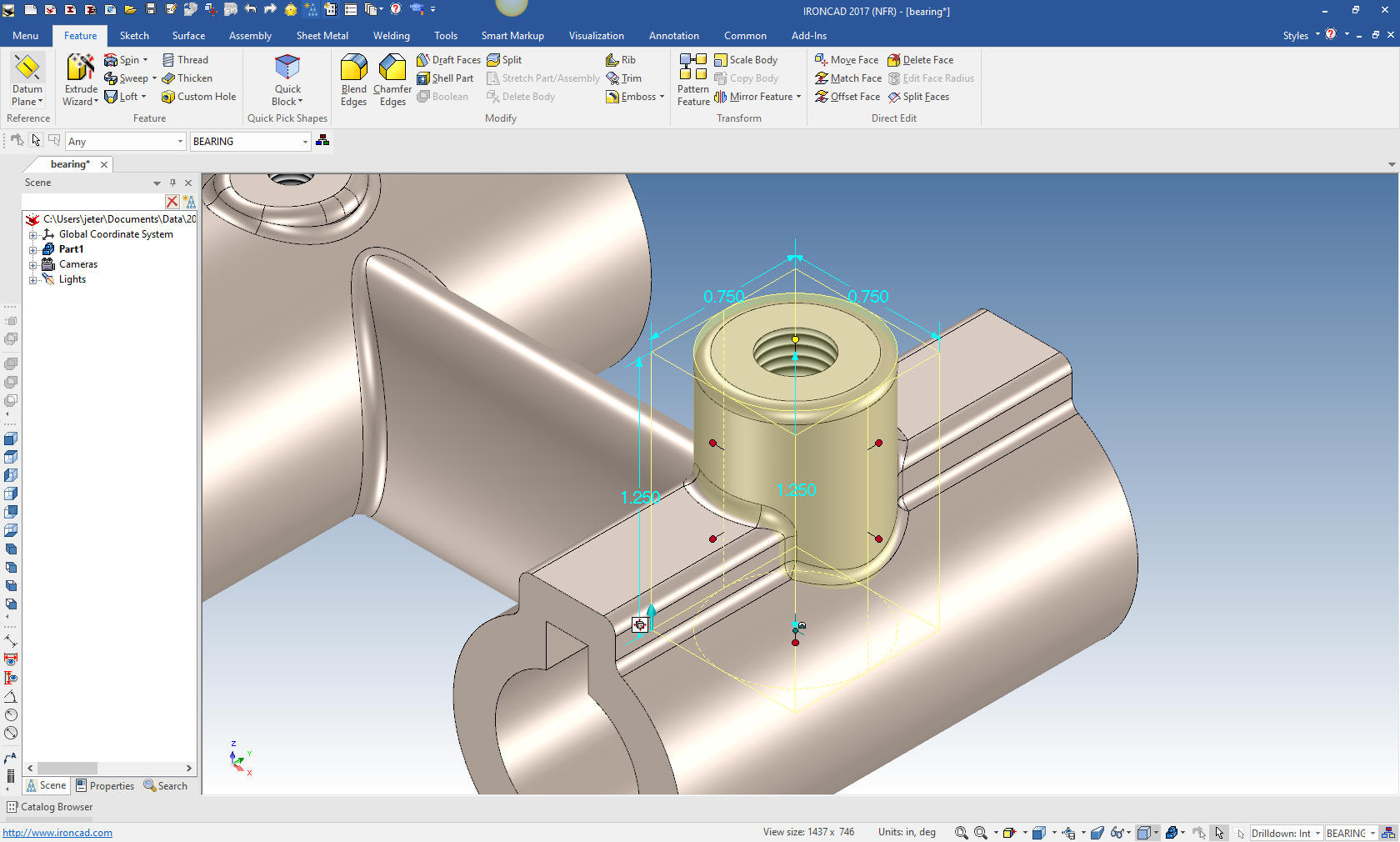
Here
we go all correct and ready for the drawing.
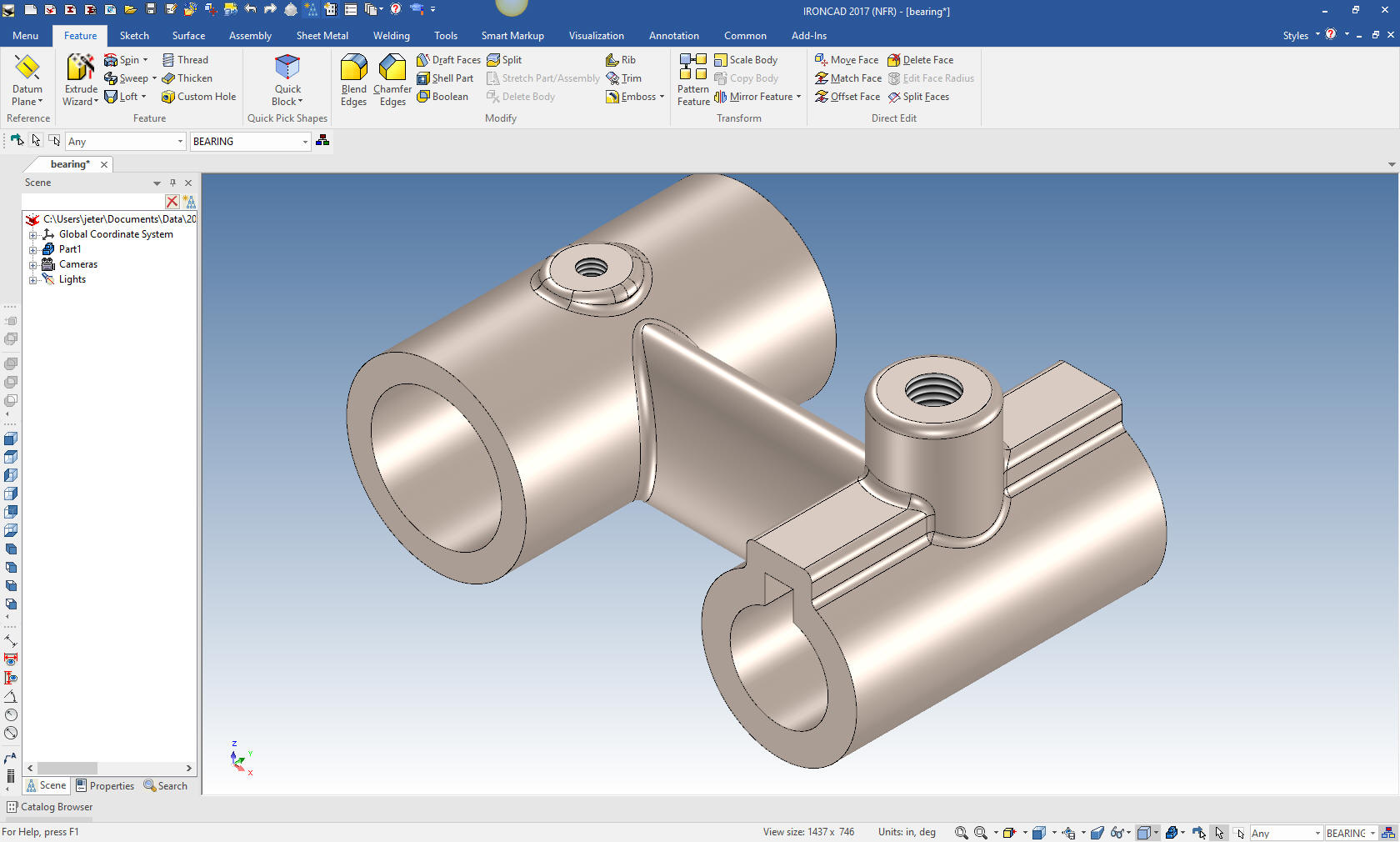
I realized we never went to the scene
browser (history tree) so I thought I would show the history of the
part. Notice that the part is highlighted. This will make more sense
as we add parts. You may have not noticed but we did not use one
sketch to create this part!
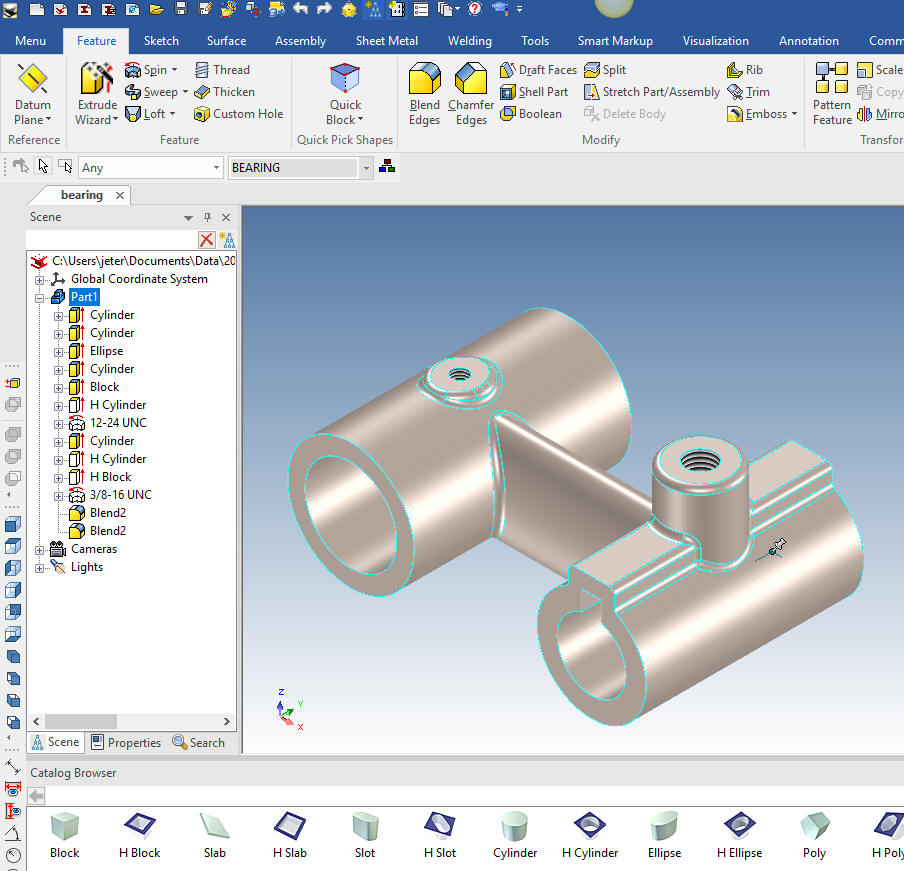
Here
is the drawing module. We will set the necessary views and scale.
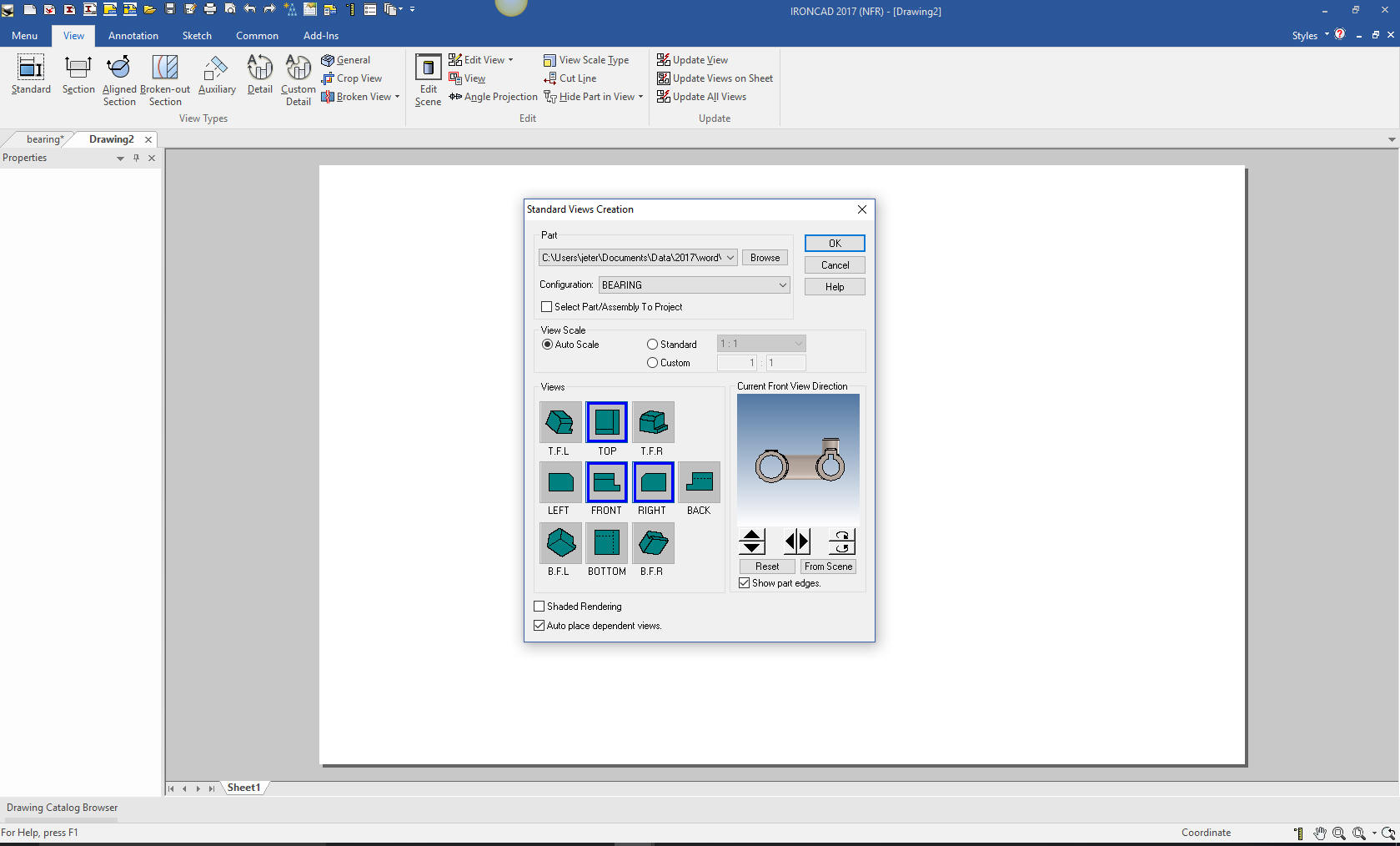
With the views in place we can now add the dimensions which is
called detailing. We just create the section view to define the
ellipse and we are done.

Here
is the original. I did add some dims that were not defined.
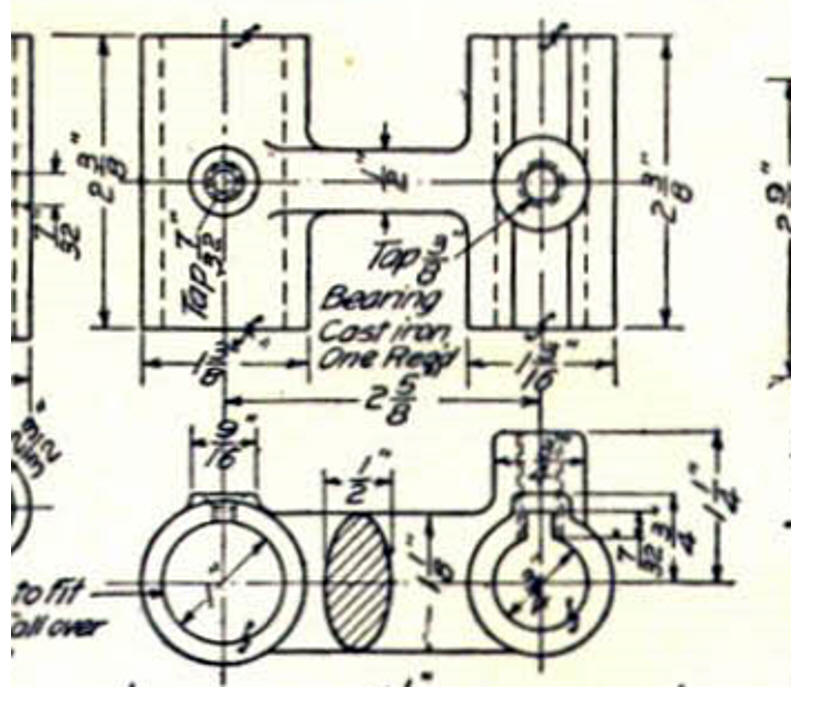
Now for lesson two:
3D Modeling Techniques IronCAD Lesson Two
If you would like
to try IronCAD, please download for a 30 day evaluation.
For more information or to download IronCAD
Give me a call if you have any
questions. I can set up a skype or go to meeting to show this part
or answer any of your questions on the operation of IronCAD. It
truly is the very best conceptual 3D CAD system.
TECH-NET Engineering Services!
We sell and
support IronCAD and ZW3D Products and provide engineering
services throughout the USA and Canada!
Why TECH-NET Sells IronCAD and ZW3D
If you are interested in adding professional
hybrid modeling capabilities or looking for a new solution to
increase your productivity, take some time to download a fully
functional 30 day evaluation and play with these packages. Feel free
to give me a call if you have any questions or would like an on-line
presentation.
|